There were still a few things to figure out for the platform. The heart of the platform is two 16' beams. We tossed around all kinds of ideas: Rough sawn lumber, reclaimed beams from old buildings, built up beams, engineered beams, etc.
We knew the structure would sit out in the elements over the winter, so it had to fair well in wet weather, that ruled out a few options. We didn't want it to warp as the timber dried, that threw out the rough sawn beam idea.
After some advice from our friend Tommy who had a lot more experience doing this kind of thing then we did, we went with the built up beam idea. We'd use two 2" X 10" X 16', with a .75" layer of plywood sandwiched in between for each beam. We figured the plywood would add support to any weak points in the beam. Each beam would be suspended from two points, with about a 10' span between suspension points.
After changing our minds several times over a few months, we settled on a in-frame floor joist system. Originally Dad thought that the joists should sit on the frame, but he came around to hanging the joists inside the frame. It helped solve a few problems: the plywood floor on top of the joists would help keep the frame square removing the need for cross braces. It saved us from buying two more 16' pieces of lumber to use as joist caps. We also didn't have to worry about hurricane clips, or other methods of ensuring that the joists would stay on top of the beams.
With these decisions made, we updated the drawing, and calculated how much lumber we'd need. We decided to go with preassure treated lumber, since it would be exposed to the elements, at least for several months.
We rolled down to the local lumber yard, and spent a good amount of time picking out the straightest and strongest looking lumber. We went through every piece of lumber that was apporpriately sized.
I was amazed at how heavy treated lumber is. I was also surprised by how expensive it is. The lumber plus a bit of miscellaneous hardware totaled about $500. Ouch. Hopefully this painful trend won't continue.
Saturday, November 25, 2006
Thursday, November 23, 2006
Build Trip!
In early October, I headed back to Indiana to hopefully build the platform. There were still a few design decisions to be made, but I had a pretty good idea of what the end product would be. I was hoping that the weather would cooperate and that nobody would get hurt.

My Dad and I got started setting up a base camp near the tree. Luckily it was possible to drive within 15' of the tree, which made it easy to haul supplies to the site. We cleared out some of the underbrush near the tree so that we'd have a nice clean work area.
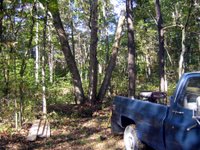
We set up about 18' of scaffolding along one side of the tree. We roped it off to one of the trunks so that there wasn't much chance of it tipping over. At first it seemed impossibly high near the top of the scaffolding, but after a few trips up and down I started to get use to it.
All 300 pounds of hardware showed up successfully. Making sure everything was there by the time I showed up required more planning than I expected. I was really nervous that I'd show up and some critical shipment wouldn't be there, and I'd lose a few days waiting for it. I was happy to see that all the heavy packages had made it OK.

My Dad and I got started setting up a base camp near the tree. Luckily it was possible to drive within 15' of the tree, which made it easy to haul supplies to the site. We cleared out some of the underbrush near the tree so that we'd have a nice clean work area.
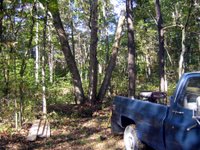
We set up about 18' of scaffolding along one side of the tree. We roped it off to one of the trunks so that there wasn't much chance of it tipping over. At first it seemed impossibly high near the top of the scaffolding, but after a few trips up and down I started to get use to it.
![]() | ![]() | ![]() |
All 300 pounds of hardware showed up successfully. Making sure everything was there by the time I showed up required more planning than I expected. I was really nervous that I'd show up and some critical shipment wouldn't be there, and I'd lose a few days waiting for it. I was happy to see that all the heavy packages had made it OK.
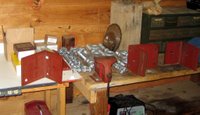
Tuesday, November 14, 2006
Designing the Platform
Next, I needed to design a sturdy platform that would both fit in the allocated space, and be a good sturdy foundation for the rest of the treehouse.
After drawing up the layout of the tree trunks on the computer, it looked like a 8' X 16' platform would fit nicely between the trunks. I originally had thought of using all 5 trunks, and perhaps making a pentagram shaped floor, but the nice square 8' X 16' platform looked larger, and much simpler to make.
The next trick was determining how to attach it to the tree. Since we'd be building in a multi-trunk tree, I had to take into account the independent movement of each trunk. I tried coming up with all kinds of sliding brackets, similar to what other people have done. The result was a lot of complicated brackets that looked expensive to make. Plus, I wasn't really sure they'd work in all possible scenarios.
One of my friends suggested suspending the entire thing via chain. The more I thought about this, the better it sounded. It would definitely solve the trunk movement problem, and I liked the idea of a suspended platform that would perhaps have more movement than a fixed point platform.
I spent a bunch of time at Mcmaster.com reading up on hardware that looked appropriate. I eventually arrived at using a combination of eyebolts, shackles, turnbuckles, and chain. I went with the largest eyebolts I could find (1" in diameter), figuring that they were going to be the weak point of the system. The eyebolts pictured below are rated at 10,000 pounds if pulled along the line of the bolt. Since I'd be pulling on them perpendicular to the bolt, they'd support significantly less weight before failing.

I didn't want to just run the eyebolts through the frame of the treehouse. I was afraid that they'd deform the wood, with all the eventual weight that'd be resting on the frame. Instead, I drew up a bunch of various right angle brackets and plates that would help distribute the load over a larger portion of the beams. After showing the various designs to my dad and other friends, I settled on some simple 1/2" thick right angle pieces, along with some 3/16" plates.
With these decisions in place, I updated the CAD drawing, and ordered a bunch of hardware. I hoped we wouldn't change too many aspects of the design once we started building, mainly because of the investment in the hardware.
After drawing up the layout of the tree trunks on the computer, it looked like a 8' X 16' platform would fit nicely between the trunks. I originally had thought of using all 5 trunks, and perhaps making a pentagram shaped floor, but the nice square 8' X 16' platform looked larger, and much simpler to make.
The next trick was determining how to attach it to the tree. Since we'd be building in a multi-trunk tree, I had to take into account the independent movement of each trunk. I tried coming up with all kinds of sliding brackets, similar to what other people have done. The result was a lot of complicated brackets that looked expensive to make. Plus, I wasn't really sure they'd work in all possible scenarios.
One of my friends suggested suspending the entire thing via chain. The more I thought about this, the better it sounded. It would definitely solve the trunk movement problem, and I liked the idea of a suspended platform that would perhaps have more movement than a fixed point platform.
I spent a bunch of time at Mcmaster.com reading up on hardware that looked appropriate. I eventually arrived at using a combination of eyebolts, shackles, turnbuckles, and chain. I went with the largest eyebolts I could find (1" in diameter), figuring that they were going to be the weak point of the system. The eyebolts pictured below are rated at 10,000 pounds if pulled along the line of the bolt. Since I'd be pulling on them perpendicular to the bolt, they'd support significantly less weight before failing.

I didn't want to just run the eyebolts through the frame of the treehouse. I was afraid that they'd deform the wood, with all the eventual weight that'd be resting on the frame. Instead, I drew up a bunch of various right angle brackets and plates that would help distribute the load over a larger portion of the beams. After showing the various designs to my dad and other friends, I settled on some simple 1/2" thick right angle pieces, along with some 3/16" plates.
![]() | ![]() |
With these decisions in place, I updated the CAD drawing, and ordered a bunch of hardware. I hoped we wouldn't change too many aspects of the design once we started building, mainly because of the investment in the hardware.

Subscribe to:
Posts (Atom)